In the dynamic landscape of the canning industry, the automatic dual – head servo can seaming machine stands out as a remarkable innovation. This advanced piece of equipment brings a host of features and benefits that are revolutionizing the way cans are sealed.
Table of Contents
Key Features
Dual – Head Design
The most prominent feature of this machine is its dual – head setup. Unlike traditional single – head seaming machines, having two seaming heads allows the machine to work on two cans simultaneously. This design significantly boosts the production capacity, enabling manufacturers to increase their output in a shorter period. For example, in a beverage canning plant, the dual – head design can double the number of cans sealed per minute, leading to a substantial increase in daily production volumes.
Servo Motor Technology
The integration of servo motors is a game – changer. Servo motors offer precise control over the seaming process. They can adjust the speed, force, and position of the seaming operation with high accuracy. This precision ensures that each can is sealed consistently, regardless of the production speed. Whether it’s a high – volume production run or a small – batch specialty canning, the servo motors maintain a uniform seal quality.
Programmable Settings
The automatic dual – head servo can seaming machine comes with programmable settings. Operators can easily input specific parameters for different can sizes, materials, and seaming requirements. This flexibility allows the machine to adapt to a wide range of canning applications. For instance, it can be programmed to seam a thin – walled aluminum can with a different set of parameters compared to a thick – walled steel can.
Automatic Can Feeding and Ejection
To streamline the production process, the machine is equipped with an automatic can feeding and ejection system. Cans are fed into the seaming area in a continuous and orderly manner, and once the seaming is complete, they are automatically ejected. This reduces the need for manual handling, minimizing the risk of damage to the cans and increasing the overall efficiency of the production line.
Real – Time Monitoring and Diagnostic System
Another valuable feature is the real – time monitoring and diagnostic system. This system continuously monitors the machine’s performance, including seaming force, speed, and can alignment. It can detect any abnormalities or potential issues in real – time and provide alerts to the operators. This proactive approach helps prevent breakdowns and reduces downtime, ensuring smooth and uninterrupted production.
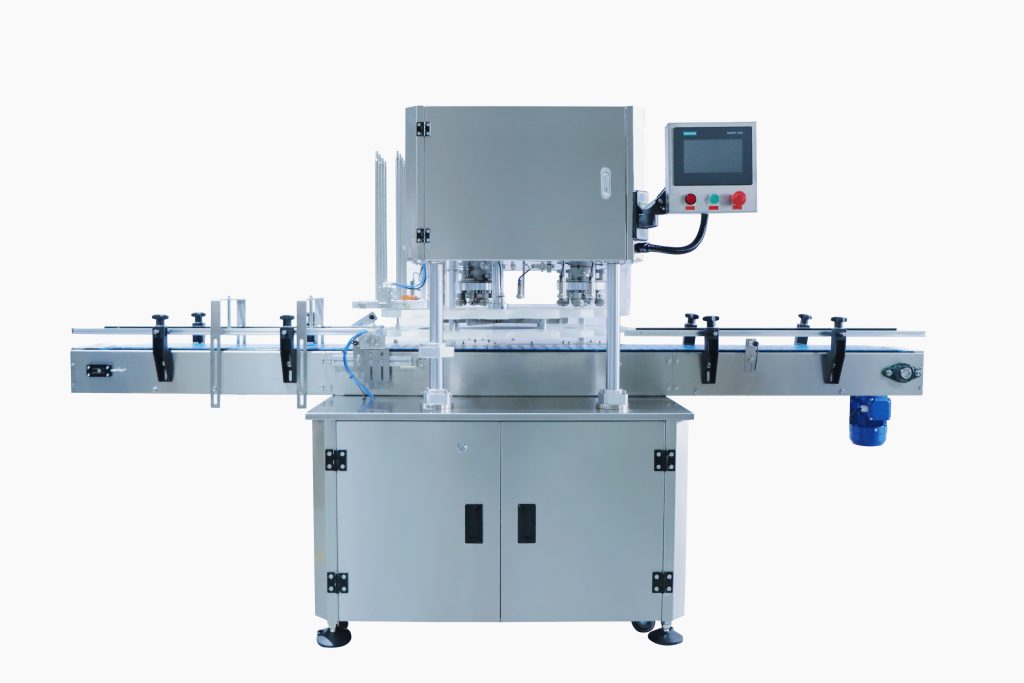
Benefits
Increased Productivity
As mentioned earlier, the dual – head design and automatic features of the machine lead to a significant increase in productivity. Manufacturers can produce more cans in less time, which is crucial for meeting market demands. Higher productivity also allows companies to take on larger orders and expand their business opportunities.
Enhanced Quality Control
The precision provided by the servo motor technology and the programmable settings ensures consistent and high – quality seals. This reduces the number of defective cans, which in turn improves the overall product quality. A high – quality seal is essential for preserving the freshness and integrity of the can’s contents, enhancing consumer satisfaction and brand reputation.
Cost Savings
The increased productivity and reduced waste associated with the machine result in cost savings. With fewer defective cans, there is less waste of raw materials. Additionally, the energy – efficient servo motors consume less power compared to traditional motors, lowering the operational costs. Over time, these savings can have a substantial impact on the company’s bottom line.
Flexibility and Adaptability
The ability to program different settings makes the machine highly flexible and adaptable. It can handle a variety of can sizes, shapes, and materials, allowing manufacturers to diversify their product offerings. This flexibility is especially valuable in a market where consumer preferences are constantly changing.
Ease of Operation and Maintenance
The user – friendly interface and the real – time monitoring system make the machine easy to operate. Even operators with limited technical skills can quickly learn how to use the machine. The modular design of the machine also simplifies maintenance. Components can be easily accessed and replaced, minimizing downtime during maintenance and repair.
In conclusion, the automatic dual – head servo can seaming machine is a powerful tool for the canning industry. Its unique features offer numerous benefits that can help manufacturers improve their productivity, quality, and profitability. By understanding and leveraging these features, companies can stay ahead in the competitive canning market.