The technology behind magnetic pump filling systems is a complex yet fascinating combination of mechanical and electronic elements that work in harmony to ensure efficient and accurate liquid filling.
At the core of these systems is the magnetic pump itself. This pump operates using a magnetic coupling instead of a traditional mechanical seal. The magnetic field generated allows for the transfer of torque from the motor to the impeller, creating a powerful and leak-free pumping action. This design eliminates the risk of fluid leakage, which is crucial in filling applications where contamination or spillage must be avoided.
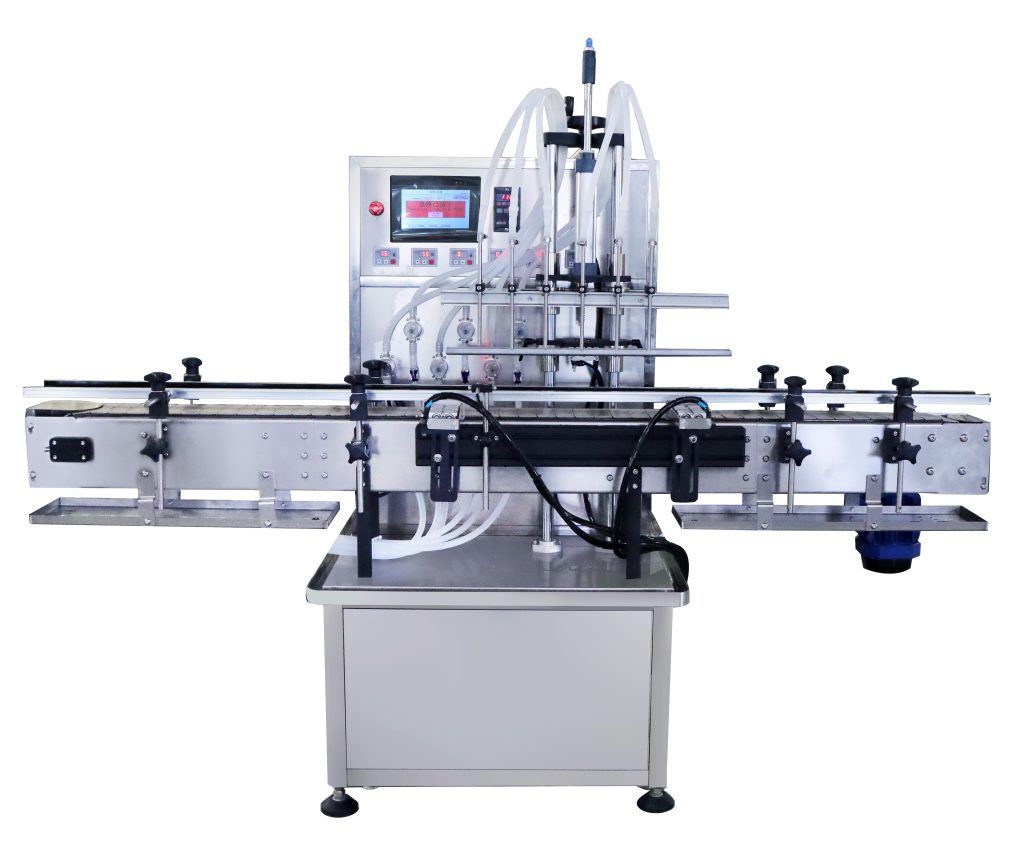
The control systems incorporated in magnetic pump filling systems are highly sophisticated. They use sensors and feedback mechanisms to monitor and adjust the flow rate, pressure, and volume of the liquid being filled. This ensures precise filling to the desired levels, regardless of variations in the liquid properties or container sizes.
The materials used in the construction of the pump and associated components are carefully selected to withstand the chemical and physical properties of the liquids being handled. This ensures durability and long-term performance without degradation or corrosion.
Advanced software and programming capabilities allow for customizable filling profiles and integration with other production line equipment. This enables seamless operation within a manufacturing facility and optimizes the overall production process.
In summary, understanding the technology behind magnetic pump filling systems involves grasping the principles of magnetic coupling, precise control mechanisms, material science, and software integration. This knowledge is essential for maximizing the efficiency and reliability of these systems in various industrial filling applications.