In the canning industry, efficiency is the key to success. It directly impacts production output, cost – effectiveness, and overall competitiveness. The automatic servo can seaming machine has emerged as a revolutionary technology that significantly enhances canning efficiency in multiple ways.
Table of Contents
High – Speed Operation
One of the most prominent features of the automatic servo can seaming machine is its ability to operate at high speeds. Traditional can seaming methods often rely on mechanical systems that have limitations in terms of speed. These systems may require time – consuming adjustments between each can seaming operation, which slows down the entire production process.
In contrast, the servo – driven technology in the automatic machine allows for rapid and continuous operation. Servo motors can precisely control the movement of the seaming components, enabling the machine to seam cans at a much faster rate. For example, in a large – scale canning factory, an automatic servo can seaming machine can seam hundreds of cans per minute, compared to the relatively slower pace of traditional machines. This high – speed operation means that more products can be produced in a shorter period, increasing the overall production capacity of the canning line.
Quick Changeover
Canning facilities often need to produce a variety of can sizes and types to meet different market demands. With traditional can seaming machines, changing over from one can size to another can be a complex and time – consuming process. It may involve disassembling and reassembling parts of the machine, as well as making multiple manual adjustments to ensure proper seaming.
The automatic servo can seaming machine simplifies this changeover process. Through its advanced programming capabilities, operators can easily input the specifications for different can sizes and types. The machine can then automatically adjust the seaming parameters, such as the pressure, speed, and position of the seaming rollers, to accommodate the new cans. This quick changeover feature allows canning manufacturers to switch between products rapidly, reducing downtime and increasing the flexibility of the production line.
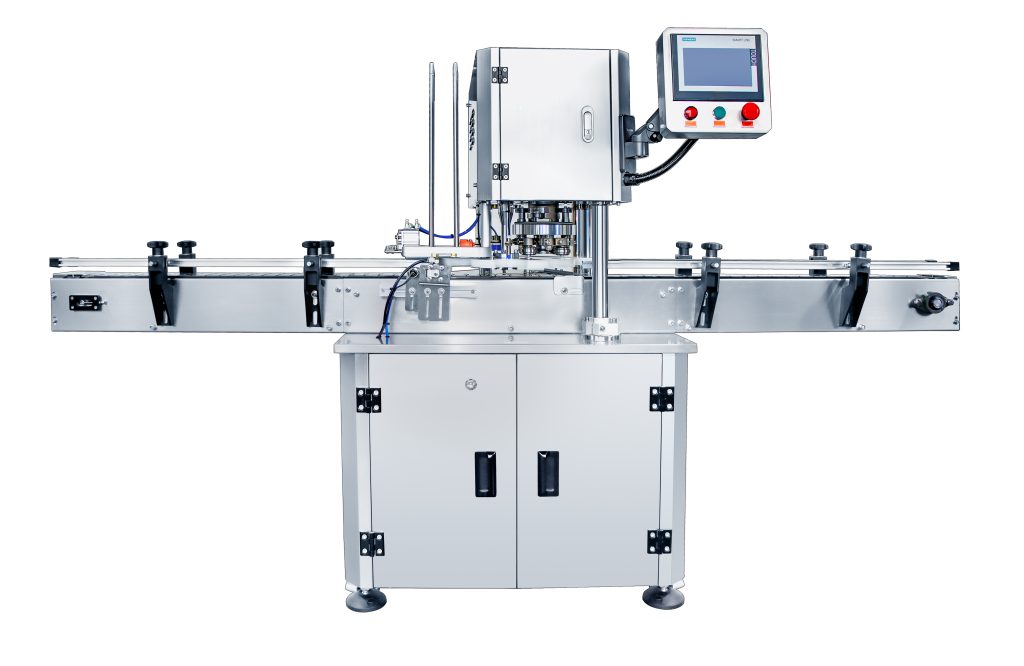
Precise Seaming and Reduced Waste
Precision is crucial in can seaming to ensure the integrity of the can and the quality of the product inside. Inaccurate seaming can lead to problems such as leakage, which not only spoils the product but also results in wasted resources.
The automatic servo can seaming machine offers exceptional precision. The servo motors can precisely control the force and movement during the seaming process, ensuring that each can is seamed with the same high – quality standard. The machine uses sensors to monitor the seaming operation in real – time and make adjustments as needed. This level of precision reduces the number of defective cans, minimizing product waste. As a result, manufacturers can save on raw materials and production costs while improving the overall quality of their canned products.
Self – Monitoring and Maintenance
In a busy canning environment, unexpected machine breakdowns can cause significant disruptions to the production schedule. Traditional machines may be difficult to monitor for potential problems, and maintenance often occurs after a breakdown has already happened.
The automatic servo can seaming machine is equipped with self – monitoring capabilities. It can continuously track the performance of various components, such as the servo motors, seaming rollers, and sensors. If any component shows signs of abnormal behavior or approaching the end of its service life, the machine can alert the operators. This proactive approach to maintenance allows for timely repairs and replacements, preventing major breakdowns and minimizing downtime. Additionally, the self – monitoring system can provide valuable data on the machine’s performance, which can be used to optimize the canning process further.
Conclusion
The automatic servo can seaming machine is a game – changer in the canning industry. Its high – speed operation, quick changeover, precise seaming, and self – monitoring features work together to enhance canning efficiency significantly. By investing in this advanced technology, canning manufacturers can increase their production output, reduce costs, improve product quality, and stay competitive in the market. As the demand for canned products continues to grow, the automatic servo can seaming machine will play an increasingly important role in meeting the industry’s needs.