In the world of product packaging, labeling accuracy is of utmost importance. A precisely placed label not only enhances the product’s aesthetic appeal but also ensures that crucial information is clearly presented to consumers. The automatic single – side labeling machine is a remarkable innovation that significantly improves labeling accuracy through several advanced mechanisms.
Table of Contents
Advanced Sensor Technology
Position Detection
One of the key ways the automatic single – side labeling machine achieves high accuracy is through its use of advanced sensors. These sensors are capable of precisely detecting the position of the product to be labeled. For example, optical sensors can identify the edges and contours of a container, whether it’s a round bottle, a square box, or an irregularly shaped item. By accurately determining the product’s position, the machine can ensure that the label is applied exactly where it should be, right in the center or at a specific pre – determined location on the single side of the product.
Label Detection
In addition to product position detection, the sensors also play a vital role in label detection. They can measure the length, width, and alignment of the label before it is applied. This ensures that the label is fed into the application process correctly and that any misaligned or defective labels are detected and rejected. For instance, if a label is slightly off – center on the label roll, the sensor can detect this and adjust the feeding mechanism to ensure proper alignment during application.
Precise Mechanical Components
Conveyor Systems
The conveyor system in an automatic single – side labeling machine is designed with great precision. It moves the products at a consistent speed and in a straight line towards the labeling station. This uniform movement is essential for accurate labeling. If the products were to move erratically or at varying speeds, it would be extremely difficult to apply the labels accurately. The conveyor system is often equipped with guides and rollers that keep the products in place and prevent any lateral movement, ensuring that the label is applied precisely on the intended side of the product.
Label Applicators
The label applicator is another critical mechanical component. It is designed to pick up the label from the label roll and apply it to the product with high accuracy. The applicator uses a combination of suction, pressure, and mechanical arms to handle the label. For example, a vacuum suction system can securely hold the label during the transfer process, preventing it from shifting or wrinkling. The mechanical arms then apply the label to the product with a controlled amount of pressure, ensuring that it adheres smoothly and evenly.
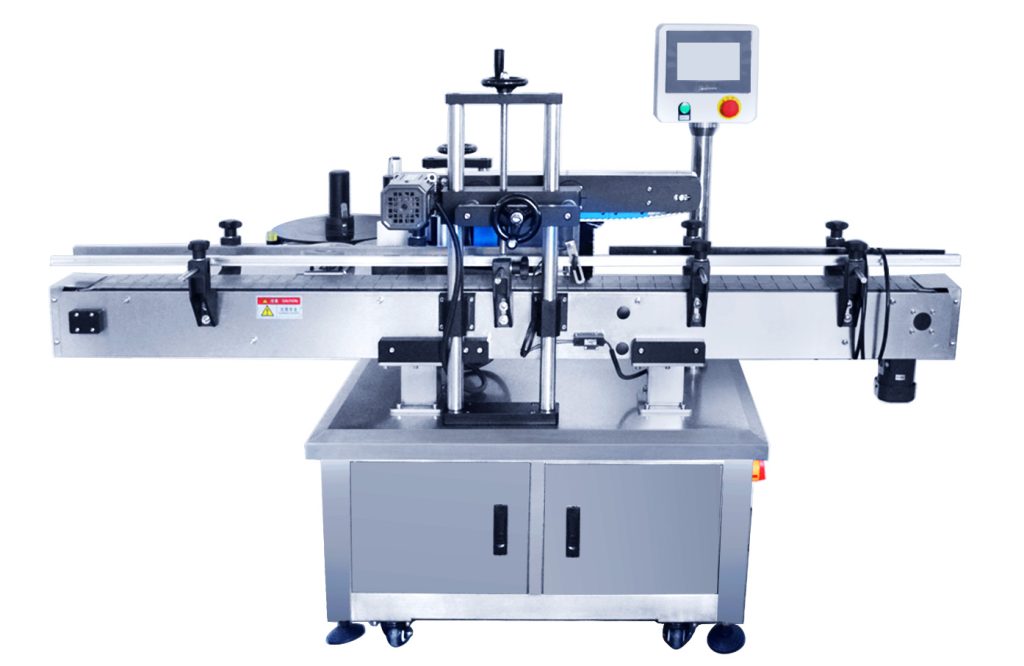
Programmable Control Systems
Customizable Settings
Automatic single – side labeling machines are equipped with programmable control systems that allow operators to set specific parameters for labeling. These settings can include the position of the label on the product, the speed of label application, and the tension of the label roll. For example, if a particular product requires the label to be placed 10 millimeters from the top edge, the operator can program this exact measurement into the control system. The machine will then apply the labels with this high level of precision for every single product.
Error Correction
The control systems also have built – in error correction mechanisms. If there is a slight deviation in the labeling process, such as a label being applied slightly off – center, the system can detect this and make real – time adjustments. It can correct the position of the label applicator or adjust the speed of the conveyor system to ensure that subsequent labels are applied accurately. This continuous monitoring and adjustment help to maintain a high level of labeling accuracy throughout the production process.
Quality Assurance Checks
Vision Inspection Systems
Many automatic single – side labeling machines are equipped with vision inspection systems. These systems use cameras and image – processing software to inspect the labeled products immediately after the labeling process. The cameras capture images of the labeled products and analyze them for any defects, such as misaligned labels, missing labels, or damaged labels. If a defect is detected, the system can trigger an alarm or reject the product from the production line. This ensures that only products with accurately applied labels are sent to the market.
Calibration and Maintenance
Regular calibration and maintenance of the automatic single – side labeling machine are also crucial for maintaining labeling accuracy. Over time, the mechanical components may wear out or the sensors may become less accurate. By performing routine calibration, operators can ensure that the machine is operating at its optimal level. Maintenance tasks, such as cleaning the sensors and lubricating the mechanical parts, also help to prevent any malfunctions that could affect labeling accuracy.
In conclusion, the automatic single – side labeling machine improves labeling accuracy through a combination of advanced sensor technology, precise mechanical components, programmable control systems, and quality assurance checks. These features work together to ensure that labels are applied accurately, consistently, and with a high level of precision, meeting the strict requirements of modern product packaging.
What are the common applications of the automatic single-side labeling machine?
How does the automatic single-side labeling machine handle different label sizes and shapes?
Can the automatic single-side labeling machine be integrated into existing packaging lines?