In the fast – paced world of modern manufacturing, packaging efficiency is a crucial factor that can make or break a business. Automatic glass bottle vacuum capping machines have emerged as a game – changer, revolutionizing the way products are packaged in glass bottles.
Table of Contents
1. Unparalleled Sealing Quality
Oxygen Removal
One of the most significant advantages of these machines is their ability to create a vacuum inside the glass bottle before capping. Oxygen is a common enemy of many products, especially those in the food, beverage, and pharmaceutical industries. In food products, oxygen can cause oxidation, leading to spoilage, loss of flavor, and a decrease in nutritional value. For example, in a bottle of olive oil, exposure to oxygen can turn the oil rancid. By removing oxygen through vacuum sealing, these machines extend the shelf – life of products, ensuring that they reach consumers in the best possible condition.
Tight and Secure Caps
Automatic glass bottle vacuum capping machines are engineered to apply caps with extreme precision. The vacuum environment inside the bottle helps to create a tight seal, preventing leaks and contamination. This is particularly important for products that are under pressure, such as carbonated beverages. A loose cap can lead to the loss of carbonation and a decrease in product quality. With these machines, each bottle is capped to the same high standard, ensuring consistent quality across the production line.
2. Dramatic Increase in Production Speed
High – Volume Capping
These machines are designed for high – volume production. They can cap a large number of glass bottles in a short period, far exceeding the capabilities of manual capping. In a large – scale bottling plant, an automatic capping machine can operate continuously, capping hundreds or even thousands of bottles per hour. This high – speed operation allows businesses to meet the demands of a large market quickly and efficiently.
Integration with Production Lines
Automatic glass bottle vacuum capping machines can be easily integrated into existing production lines. They are designed to work in harmony with other equipment, such as filling machines and labeling machines. This seamless integration ensures a smooth and continuous production process, minimizing downtime and maximizing productivity. For example, in a beverage production line, the capping machine can be synchronized with the filling machine so that as soon as a bottle is filled, it is immediately capped, reducing the overall production time.
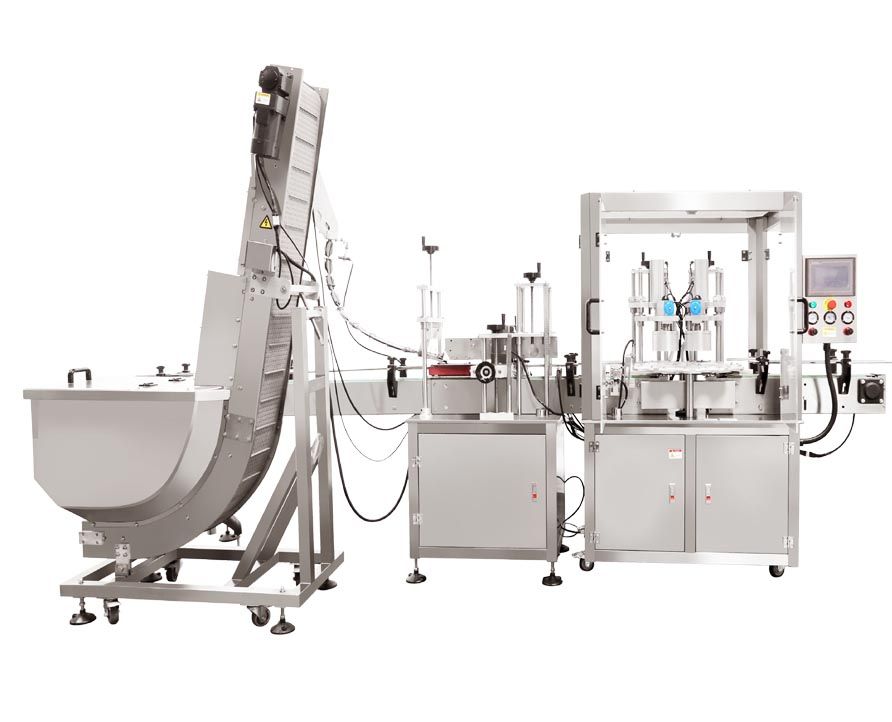
3. Labor and Cost Savings
Reduced Labor Requirements
Automating the capping process with these machines significantly reduces the need for manual labor. Manual capping is a labor – intensive and time – consuming task that requires a large workforce. With an automatic capping machine, a few operators can monitor and manage the entire capping process. This not only saves on labor costs but also reduces the risk of human error. Workers can be redeployed to other areas of the production process that require more human skills, such as quality control or product development.
Lower Maintenance and Operational Costs
Modern automatic glass bottle vacuum capping machines are built with durable and reliable components, which require less maintenance compared to older – style capping equipment. They are also designed to be energy – efficient, consuming less power during operation. This results in lower maintenance and operational costs over the long term, making them a cost – effective investment for businesses.
4. Versatility and Adaptability
Compatibility with Different Bottle Sizes and Shapes
These machines are highly versatile and can handle a wide variety of glass bottle sizes and shapes. Whether it’s a small, narrow – necked perfume bottle or a large, wide – mouthed jar, the machine can be adjusted to fit the specific dimensions. This flexibility is beneficial for businesses that produce multiple products in different packaging formats. For example, a cosmetics company can use the same capping machine for its various products, from small vials of essential oils to large bottles of moisturizer.
Ability to Use Various Cap Types
Automatic glass bottle vacuum capping machines can accommodate different types of caps, including screw caps, snap – on caps, and corks. This allows businesses to choose the most appropriate cap for their product based on factors like product type, market demand, and branding. A winery can use corks for its premium wines and screw caps for its more affordable offerings, all with the same capping machine.
5. Improved Product Safety and Hygiene
Contamination Prevention
In industries such as food, pharmaceuticals, and cosmetics, maintaining high levels of hygiene is essential. Automatic glass bottle vacuum capping machines are designed with smooth, easy – to – clean surfaces and components. The vacuum sealing process also reduces the risk of external contaminants entering the bottle, ensuring the safety and purity of the product. This is crucial for products that are consumed or applied to the body, as any contamination can have serious health consequences.
Operator Safety
These machines are equipped with advanced safety features, such as guards, sensors, and emergency stop buttons. These features protect the operators from potential hazards during the capping process, such as moving parts or flying caps. By providing a safe working environment, businesses can reduce the risk of workplace accidents and injuries.
In conclusion, automatic glass bottle vacuum capping machines are revolutionizing packaging efficiency in numerous ways. Their ability to provide high – quality sealing, increase production speed, save labor and costs, offer versatility, and improve safety and hygiene makes them an essential tool for businesses in the glass – bottle packaging industry. As technology continues to advance, these machines are likely to become even more efficient and effective, further transforming the packaging landscape.